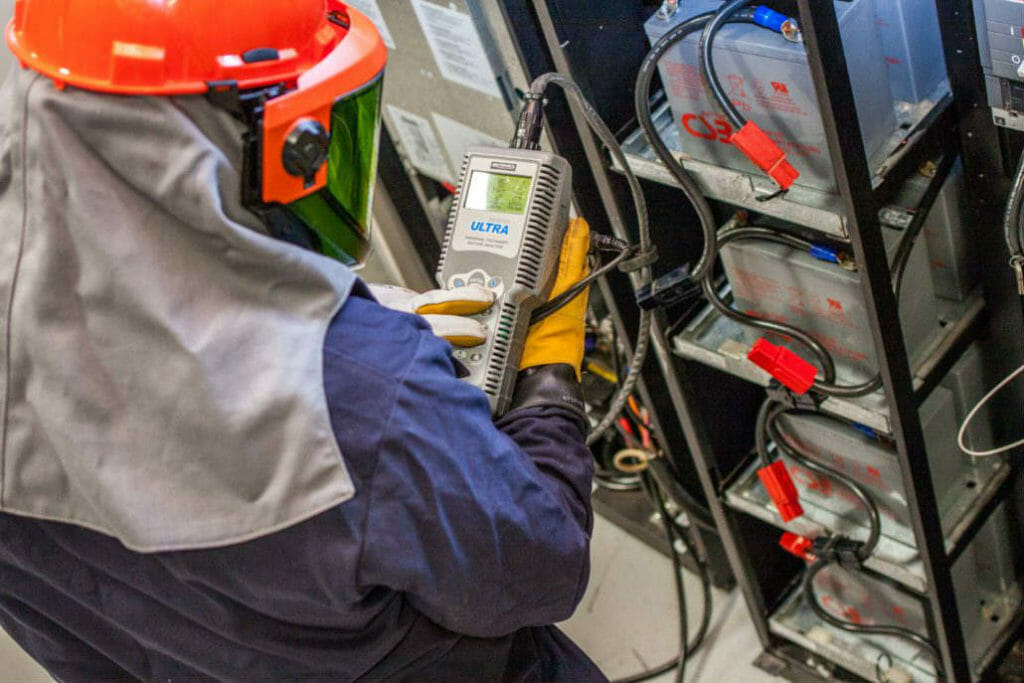
Importance of Power Plant Maintenance
In our last article, we discussed DC power plants, what they are, and how they are often used. Just like any back-up power system, DC power plants need regular service checks and maintenance performed to work optimally. It is important to state that DC plants, although similar to the function of UPS systems, have many functional differences and require unique training when performing annual maintenance. During a preventative maintenance visit a technician will usually isolate individual rectifiers and charging components to evaluate function and longevity. This practice helps to reduce the risk of a potential failure before it happens.
Many DC power plants consist of multiple parallel-redundant rectifiers that convert AC power to DC power, charge batteries, and supply DC Power, often in 24 or 48V to critical load equipment. These plants are often chosen for critical systems in industries such as the telecom industry for their long battery support times. These support times can range from 1 to over 24 hours, with a typical range between 3 and 8 hours.
It then makes sense that the two most critical parts of DC power plant maintenance center on:
- Rectifiers
- Batteries
Rectifiers need to be consistently monitored and maintained to make sure they are operating optimally. Just as with UPS maintenance, annual maintenance is critical, but up to quarterly maintenance may be needed, depending on how critical the infrastructure might be. Routine maintenance will help increase Mean Time between Failures, or (MTBF.)
When performing rectifier maintenance, all system components of the rectifier need to be analyzed for potential issues. This includes inspection of some of the following components and services:
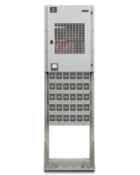
- Cooling Fans
- Circuit Breakers and Other Assemblies
- Check and tighten terminal connections
- Verify proper float voltage
- Measure input / output voltage and calibration
- Thermographic Scan
Many breakdowns with rectifiers are related to aging, lightning strikes, and neglect of cooling fans and batteries. Common issues include:
- faulty meters
- blown fuses
- loose terminals
- external damage (weather related)
Careful inspection and care of the rectifier can reduce or eliminate these issues, as well as other issues like load imbalances and hot spots.
We discussed in our previous article that many DC power plants use either VRLA or Wet Cell batteries that are typically front access batteries. Regular battery maintenance and replacement is critical to a DC power plant, which has a consistent power draw. Regular maintenance and replacement will avoid issues such as degradation or corrosion. Degradation or corrosion can be caused by:
- Overcharging batteries. This can cause degradation and eventual failure of the battery. Consistent overcharging can cause thermal runaway, where continuous rising temperature and rising current result in battery case rupture or possible fire.
- Discharge cycle issues. Batteries are typically rated for a certain number of deep and shallow discharges. Battery life expectancy is affected by load during discharge, rate of discharge, length of discharge, rate of recharge, and recharge time. A larger than warranted number of deep discharges can stress the battery more than a partial discharge.
- High ambient temperatures. If temperatures in the room where the plant is stored are higher than the manufacturer’s recommendations, it reduces the life expectancy of the batteries.
- DC plant batteries, although similar to VRLA batteries, can vary greatly in their life expectancy. Environmental conditions, frequency of discharge, manufacturing quality and other factors can impact the number of useful years a battery will last. Because of the life cycle associated with these batteries, the expense and attention to maintenance can greatly impact your investment over time.
Telecommunications companies’ infrastructure has changed dramatically over the past decade. With the advent of fiber to the customer premise this has impacted the traditional use of DC Plants in traditional copper last mile infrastructure. These changes have given telecommunications professionals and ISP providers a great chance to reduce load and reevaluate the role of their existing DC plants in their facility. QPS can evaluate current infrastructure to reduce power consumption and help with technology migrations.

Contact QPS to make sure your DC power plant maintenance is done right.
Published on May 24 2018
Last Updated on Oct 17 2023